In the field of DTF (Direct to Film) printing, the proper handling of white ink plays a crucial role in both print quality and equipment maintenance. To fully utilize the effectiveness of white ink, it is essential to have an in-depth understanding of its characteristics, master scientific usage and storage methods, and effectively address issues such as nozzle clogging.
I. Analysis of the Characteristics of White Ink
Compared with colored inks, white ink has a unique chemical composition. Its main components typically include white pigments such as titanium dioxide. Titanium dioxide, with its excellent whiteness, covering power, and chemical stability, is a key pigment component in white ink. To ensure the uniform dispersion of pigments, various high-molecular polymer dispersants are added. One end of these dispersant molecules adsorbs on the surface of pigment particles, while the other end has an affinity for the solvent, enabling the pigment particles to be stably suspended in the ink. Meanwhile, the solvent system is mainly water, supplemented with an appropriate amount of alcohol, ether, and other organic solvents to adjust the evaporation rate and fluidity of the ink, ensuring that during the printing process, the ink can be smoothly ejected from the nozzle and quickly dry and solidify on the printing medium.
II. Key Points for Using White Ink
(I) Precise Preparation Before Printing
- Shake Thoroughly: The pigment particles in white ink have a relatively large specific gravity and are prone to sedimentation when left standing. Therefore, it is necessary to shake the ink bottle thoroughly before use. This can be achieved by using professional shaking equipment for several minutes. If such equipment is unavailable, manually inverting the ink bottle multiple times is also essential to evenly mix the pigment with the solvent, additives, and other components, ensuring consistent print colors.
- Accurate Filtration: To remove possible impurities and agglomerates, it is necessary to select a suitable mesh filter for filtration. A filter with a mesh size between 100 and 200 meshes is preferred to ensure that the ink flowing into the cartridge is pure and free from clogging the tiny nozzle holes.
(II) Reasonable Setting of Printing Parameters
- Temperature and Humidity Control: The ambient temperature and humidity are the “hidden controllers” of the printing effect of white ink. Maintaining a temperature range of 20°C – 25°C and a humidity range of 40% – 60% is ideal. The temperature can be adjusted using an air conditioner, and the humidity can be balanced using a humidifier or dehumidifier. Under such environmental conditions, the physical properties of white ink, such as viscosity and surface tension, are stable, facilitating precise printing.
- Nozzle Height Adjustment: The distance between the nozzle and the printing medium needs to be precisely controlled, with a suitable range of 1.5 mm – 3 mm. If the distance is too high, the ink will be affected by air resistance, resulting in large landing deviations and impaired precision. If the distance is too low, the medium may be scratched, damaging the nozzle and print quality.
- Printing Speed Optimization: Considering the fluidity of white ink and the performance of the printer, it is reasonable to reduce the printing speed. Generally, setting the printing speed within the range of 30% – 60% and determining the optimal value through repeated tests ensures that the ink is evenly and sufficiently adhered to the medium.
III. Storage Tips for White Ink
- Temperature and Light Control: The storage environment is the key to “preserving” white ink. It should be placed in a cool, dry, and dark place, with a temperature range of 5°C – 25°C. Direct sunlight or high temperatures can cause the ink to deteriorate, dry out, and its chemical properties to degrade. A dedicated ink storage cabinet equipped with light-shielding facilities is an ideal choice.
- Sealing Protection: When not in use, be sure to tighten the ink bottle cap to block air. Oxygen can cause the ink to oxidize, and water evaporation can change the concentration and performance of the ink. If possible, fill the bottle with inert gases such as nitrogen to enhance protection.
IV. Strategies for Dealing with Nozzle Clogging
- Routine Daily Cleaning: Regularly cleaning the nozzle is a “compulsory course” for preventing clogging. Every 2 – 3 days, start the nozzle cleaning program through the printer software. If the clogging is slightly severe, soak the nozzle in a special nozzle cleaning solution. Carefully remove the nozzle and place it in a container with the cleaning solution for 1 – 2 hours, then rinse it clean with clean water to restore the nozzle’s patency.
- Ultrasonic Deep Cleaning: To deal with stubborn clogging, an ultrasonic cleaner comes in handy. Gently place the nozzle into the machine, add an appropriate amount of cleaning solution, set the power to 300W – 500W, and the time to 5 – 10 minutes. However, it should be noted to be careful not to exceed the power and time limits to avoid damaging the precise structure of the nozzle.
V. Advanced Equipment Features of KEDITEC DTF Printers
Keditec’s DTF printers are equipped with an innovative white ink circulation and agitation system. This system comprises two levels of agitation: a primary level of stirring and a secondary level of tumbling. The primary stirring ensures that the white ink is constantly and gently mixed, preventing the pigment particles from settling at the bottom of the ink reservoir. The secondary tumbling action provides a more vigorous agitation, further homogenizing the ink and enhancing its overall quality. In combination with an automatic humidification system, these features work together to significantly reduce the precipitation of white ink. The automatic humidification system helps maintain the appropriate moisture content within the ink, keeping its viscosity and fluidity in an optimal state. This not only extends the usable life of the white ink but also ensures consistent print quality throughout the printing process.
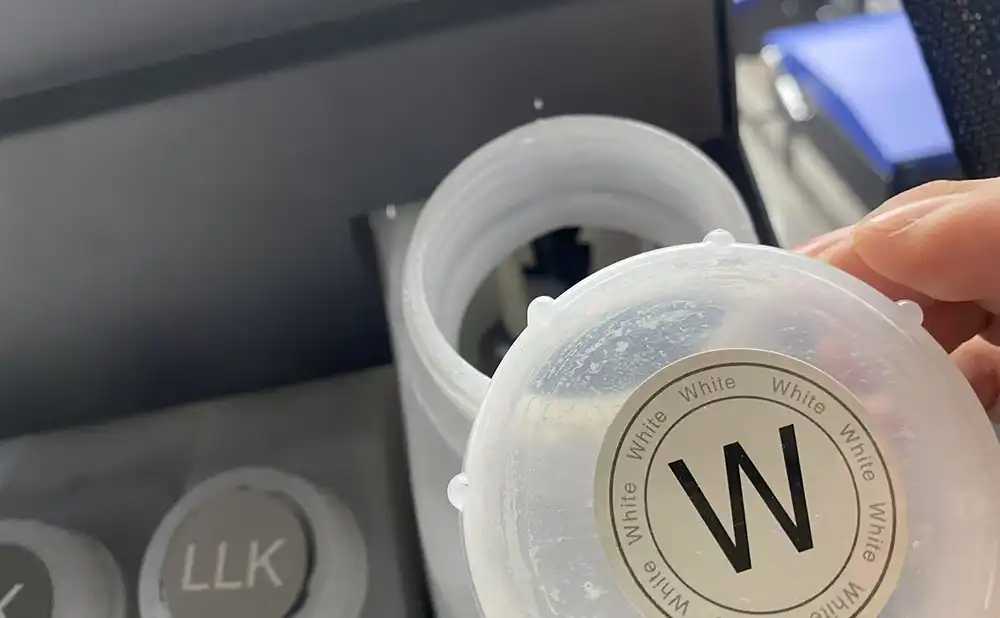
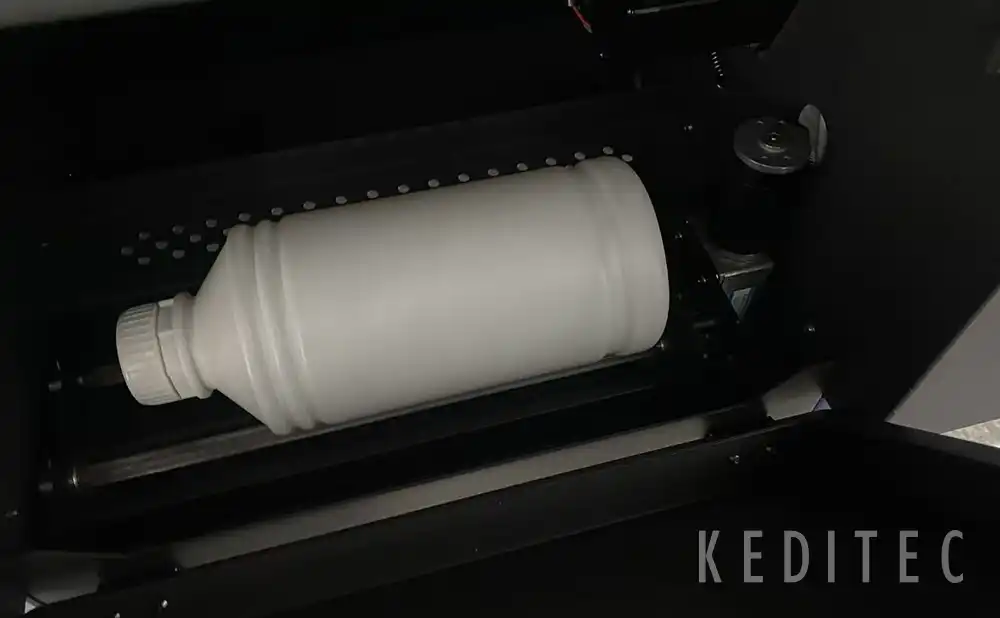
In conclusion, mastering comprehensive knowledge of white ink in DTF printers, from usage to storage and to nozzle clogging treatment, is the core point for ensuring smooth printing and improving print quality, laying a solid foundation for the efficient operation of DTF printing business.